NVIDIA and Taiwan’s manufacturing ecosystem, including Delta Electronics, Foxconn, TSMC and Wistron, are showcasing this week at COMPUTEX in Taipei the crucial role digital twins play in accelerating industrial AI.
These electronics, semiconductor and robotics manufacturing leaders are using Universal Scene Description (OpenUSD) and NVIDIA Omniverse libraries and blueprints to develop physically based digital twins. This is transforming factory planning by unlocking new operational efficiencies and accelerating the development, testing and validation of autonomous robots and robotic fleets.
Many of these manufacturers are also extending the digitalization of their factories to the real world, using the NVIDIA AI Blueprint for video search and summarization (VSS) — now generally available and part of the NVIDIA Metropolis platform — to deploy video analytics AI agents into their operations and drive additional automation and optimizations in defect detection and other operations.
Taiwan Manufacturers Optimize Planning and Operations With Simulation and AI Agents
Taiwan’s leading electronics and semiconductor manufacturers are using digital twins, physically based simulation and AI agents to optimize existing operations and vastly accelerate the planning and commissioning of new factories.
Foxconn is leading the way. At its Taiwan facilities, Foxconn engineers rely on the Fii Digital Twin platform, developed with OpenUSD, Siemens and Omniverse technologies, to design and simulate robot work cells, assembly lines and entire factory layouts.
These digital twins connect to material control systems and use Autodesk Flexsim, NVIDIA cuOpt and NVIDIA Isaac Sim to enable engineers to simulate and dynamically optimize the flow of materials, equipment, autonomous mobile robots (AMRs), automated guided vehicles, and other robots and humans. By developing a standard digital twin model for their factories, Foxconn can quickly migrate and easily reconfigure its designs and plans for new factory deployments.
Foxconn is using the NVIDIA Isaac GR00T N1 model, the NVIDIA Isaac GR00T-Mimic blueprint for synthetic manipulation motion generation and NVIDIA Isaac Lab to train industrial manipulator arms and humanoid robots for performing complex tasks such as screw-tightening, pick and place, assembly and cable insertion. Foxconn robotics developers use the Mega NVIDIA Omniverse Blueprint to simulate and test large robotic fleets comprising AMRs, manipulators and humanoid robots before deploying them in facilities.
To accelerate analysis and decision-making, Foxconn engineers use their digital twin platform to conduct thermal assessments of POD rooms across different scenarios. By connecting their digital twins to the Cadence Reality Digital Twin Platform and integrating NVIDIA PhysicsNeMo frameworks, teams can conduct thermal simulations 150x faster, reduce thermal risks and identify energy-saving opportunities.
Using the Omniverse Blueprint for AI factory digital twins, Foxconn can simulate and test GB200 Grace Blackwell Superchips in liquid-cooled PODs to replicate the conditions of an AI factory.
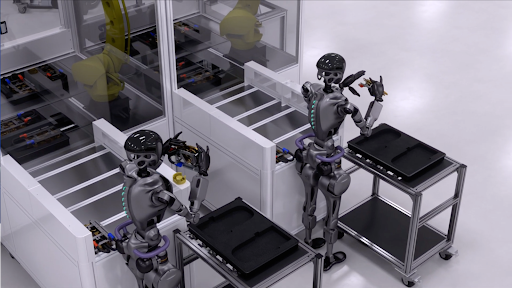
The company is also deploying video analytics AI agents using the VSS blueprint from NVIDIA Metropolis for real-time video analysis and insights in live production scenarios.
TSMC is collaborating with an AI-powered digital twins startup to optimize the planning and construction of its new fabs. TSMC taps into an AI engine and applications built with Omniverse libraries to transform traditional 2D computer-aided designs into rich, interactive 3D layouts of their complex facilities, including specialized areas like clean rooms.
Visualizing these optimized layouts in a digital twin allows planning teams to proactively identify and resolve equipment collisions, understand system interdependencies, and assess impacts on space and operational key performance indicators.
This AI-driven approach is enhanced by NVIDIA cuOpt for optimization and reinforcement learning with NVIDIA Isaac Lab, enabling the generation of intricate, multilevel piping systems in seconds — a task that traditionally requires substantial time and effort. This enables engineers to virtually validate complex pipe routing and drastically reduce design revisions, ultimately streamlining the entire fab development process.
TSMC also uses vision language models and vision foundation models to improve automated defect classification workflows — boosting efficiency to classify wafer product defects for engineers to pinpoint potential root causes for the issues. Beyond the use of digital twins and vision AI, TSMC also taps into NVIDIA CUDA-X software libraries and NVIDIA GPUs to accelerate its entire semiconductor chip design workflow — from lithography with NVIDIA cuLitho to semiconductor process simulation.
Wistron teams drive operational efficiencies, optimize layout planning of their plants, and train robots and workers with the Wistron Digital Twin (WiDT) platform. The platform is powered by software from Autodesk, Cadence and Microsoft and taps into NVIDIA AI and Omniverse libraries.
By connecting the WiDT platform to generative AI tools and real-time data from surface mount technology machines and shopfloor control systems, operations teams can visualize real-time dashboards to quickly diagnose and improve machine and plant performance.
Wistron robotics developers use the platform, and its integration with NVIDIA Isaac Sim, to simulate and test robotic arms. With a simulation-first approach, teams reduced the time needed for each arm to assemble parts on the production line by 12 seconds.
The Wistron digital twin platform also uses the VSS blueprint to create and curate training videos for teaching workers how to perform and manage complex tasks and scenarios. The platform uses NVIDIA Cosmos Tokenizer to help teams analyze and break down worker actions on the production line and improve standard operating procedures. This approach is enabling Wistron to accelerate onboarding, improve worker productivity and ensure safety.
Wiwynn uses AI-enabled digital twins built with Omniverse technologies to optimize factory layouts, simulate production, integrate cobots and enhance quality control through improved inspection and analysis. These solutions have driven significant manufacturing and logistics innovation and efficiencies.
Pegatron’s PEGAVERSE and PEGAAi platforms equip engineers and factory managers with digital twins that support many use cases, including factory planning, predictive maintenance, process optimization, resource planning, remote monitoring and quality control.
Teams also use the platforms to build visual AI agents to help workers perfect complex assembly tasks. These AI agents, developed with the NVIDIA AI Blueprint for VSS and NVIDIA Metropolis, have enabled Pegatron to augment assembly processes, reduce labor costs by 7% and decrease assembly line defect rates by 67%.
Kenmec and MetAI are using Omniverse technologies and the Mega NVIDIA Omniverse Blueprint to build physically accurate digital twins for simulating, testing and deploying warehouse automation solutions. Together, the teams virtualized the entire Chief Smart Logistics Center, creating a full-fidelity simulation environment that brings together physical dynamics, real-time controller logic, AI-driven testing and optimization — all within a simulated environment.
GIGABYTE operations teams are using digital twins developed with Omniverse libraries and connected to live IoT data from the manufacturing floor to improve operational monitoring of production systems. By visually flagging anomalies, including equipment issues and delays, the digital twins help teams quickly identify issues, conduct root cause analysis and take corrective actions.
Quanta Cloud Technology engineering, operations and logistics teams collaborate using digital twin solutions built with Omniverse to accelerate factory planning. Digital twins provide these cross-functional teams with access to the latest design data, enabling them to provide immediate feedback on proposed layouts, which leads to optimized workflows and improved space utilization. Teams can further extend collaboration sessions to external customers and suppliers so they can remotely contribute to design reviews and validation.
Manufacturers Embrace Digital Twins to Accelerate Robotics Development
In addition to creating the future in manufacturing, Taiwan manufacturers are using digital twins, powered by Omniverse libraries and blueprints, to develop the next wave of AI-enabled robots.
Delta Electronics is using Isaac Sim to optimize electronic component production and to simulate, train and validate its entire range of industrial robots — from AMRs to industrial manipulators.
The company is transforming its expertise into a service by designing a cyber-physical integrated classroom to be launched soon in Taiwan, where customers learn to use the DIATwin platform to simulate and integrate Delta’s industrial equipment and robots to ensure a more effective implementation into their own production lines.
Techman Robot is advancing intelligent automation at Volkswagen’s Transparent Factory. Using Isaac Sim, Techman’s AI Cobots learn to operate on GESSbot AMRs in physically accurate simulations to perform real-time assembly, inspection and adaptive manipulation tasks with precision. By simulating robot behavior and workflows virtually, Techman Robot has reduced the time to program robots by 70% and improved robot productivity by 20%.
Foxlink is using the Isaac GR00T N1 model to add generalized intelligence and autonomy to its industrial robots used in manufacturing facilities.
Solomon’s AI vision solution, powered by NVIDIA Isaac Manipulator CUDA-X acceleration libraries, is helping Inventec significantly accelerate its robotic server inspection process by boosting complex motion planning speed by up to 8x and reducing errors by 50%.
Kudan is integrating its Visual SLAM technology with Isaac Perceptor CUDA-X acceleration libraries into NexAIoT’s AMR, NexMOV-2. This integration uses advanced 3D perception and navigation, enabling them to navigate complex, unstructured environments such as manufacturing, logistics and healthcare facilities with greater precision and reliability.
MSI is powering its industrial robots with the NVIDIA Jetson AGX Orin module to perform a variety of tasks, from pick-and-place and material handling to delivering payloads inside large warehouses and facilities.
In healthcare, Adata and Advantech are jointly using Isaac Sim, Isaac Perceptor and Jetson Orin to develop AMRs for disinfecting hospitals. This collaboration has reduced deployment time by 70% and made the disinfection process 3x faster. Ubitus is also using the Isaac platform to train G1 humanoid robots to deliver medical checkup materials and specimens, helping alleviate labor shortages in hospitals.
Learn more by watching the COMPUTEX keynote from NVIDIA founder and CEO Jensen Huang and attending sessions at NVIDIA GTC Taipei, running through May 22.
See notice regarding software product information.
Featured image courtesy of Quanta (top left), Wistron (top right), Foxconn (bottom left), Pegatron (bottom right).